Train your team to think critically, not just memorize tools
Sustainable improvement isn’t about checklists or templates. It takes the right mindset and meaningful data to uncover real insights. Most improvement programs fall short because they teach a list of tools or a rigid process. Problem solving is a winding, iterative journey of learning. If the problem were easy, it’d already be solved.
I help teams develop critical thinking and practical problem-solving skills through in-person, hands-on training. They learn to ask the right questions, collect and analyze the data that matters using statistical methods, and make changes that last. Invest in your team to:
Think critically, not just execute
Ask the right questions that drive disruptive discovery
Eliminate waste by focusing on what truly matters
Make smarter decisions grounded in data
Prevent harmful process tampering with process behavior charts
Run structured experiments to learn faster
Deliver lasting, measurable results
What you’ll learn to do
-
Question.
Great problem-solving starts with direct observation and thoughtful inquiry. If you want new answers, you need to ask new questions.
In this program, you’ll learn to see what’s actually happening by going to where the work gets done and being a perceptive observer. Whether your in manufacturing, design, or transactional services the approach still applies.
You’ll use visual tools to map not just the process or product, but also your thinking. Most importantly, you’ll build the habit of curiosity—an insatiable drive for discovery, experimentation, and meaningful results.
-
Learn.
Understanding a system isn’t about luck, it’s a skill you can build. In this program, you’ll learn how to use data, and thoughtful experimentation to uncover what’s really driving results, not just what appears on the surface.
We’ll walk through statistical thinking: how to validate your measurement system and then use it to collect meaningful data, separate signal from noise, and determine the y=f(x) of your system.
You’ll accomplish this through the use of improved observation and directed experimentation that move you from guessing to knowing.
-
Improve.
Anyone can make a change, but this program teaches you how to make the right change and then prove it works. You’ll learn to test improvements under real-world conditions, measure their impact, and use data to build confidence and gain support from stakeholders.
You’ll also explore how to spot potential risks or unintended consequences early, so you don’t fix one area only to create problems in another.
Sustaining improvement means fighting entropy with strong and proactive controls. You’ll learn how to lock in gains and prevent backsliding turning wins into lasting success.
How you’ll do it
Improvement won’t happen in a single study. It’s a disciplined sequential way of working.
You’ll learn how to move through cycles of action and reflection using PDSA (Plan-Do-Study-Act), applying principles like Keep It Small and Sequential to make fast, low-risk progress.
We’ll work in a rhythm of induction and deduction, building understanding through rapid learning loops. Along the way, you’ll develop simple, effective project management habits that keep your efforts organized, focused, and grounded in results.
Where to focus your efforts
Improvement only matters if it happens in the right place. You’ll learn to focus your effort where it creates measurable business value. By listening to the Voice of the Customer, the Voice of the Process, and the Voice of the Business, you’ll be equipped to implement the kind of change that meets the needs of all stakeholders.
Using the mapping and questioning techniques we cover, you’ll sharpen your skills as a perceptive observer to be able to see what matters, not just what’s visible. Systems thinking helps ensure your improvements serve the whole, not just a part.
By applying the 80/20 rule and studying the variation, you’ll target the critical few inputs that drive most of the outcomes. Because effective improvement starts with choosing the right problems to solve.
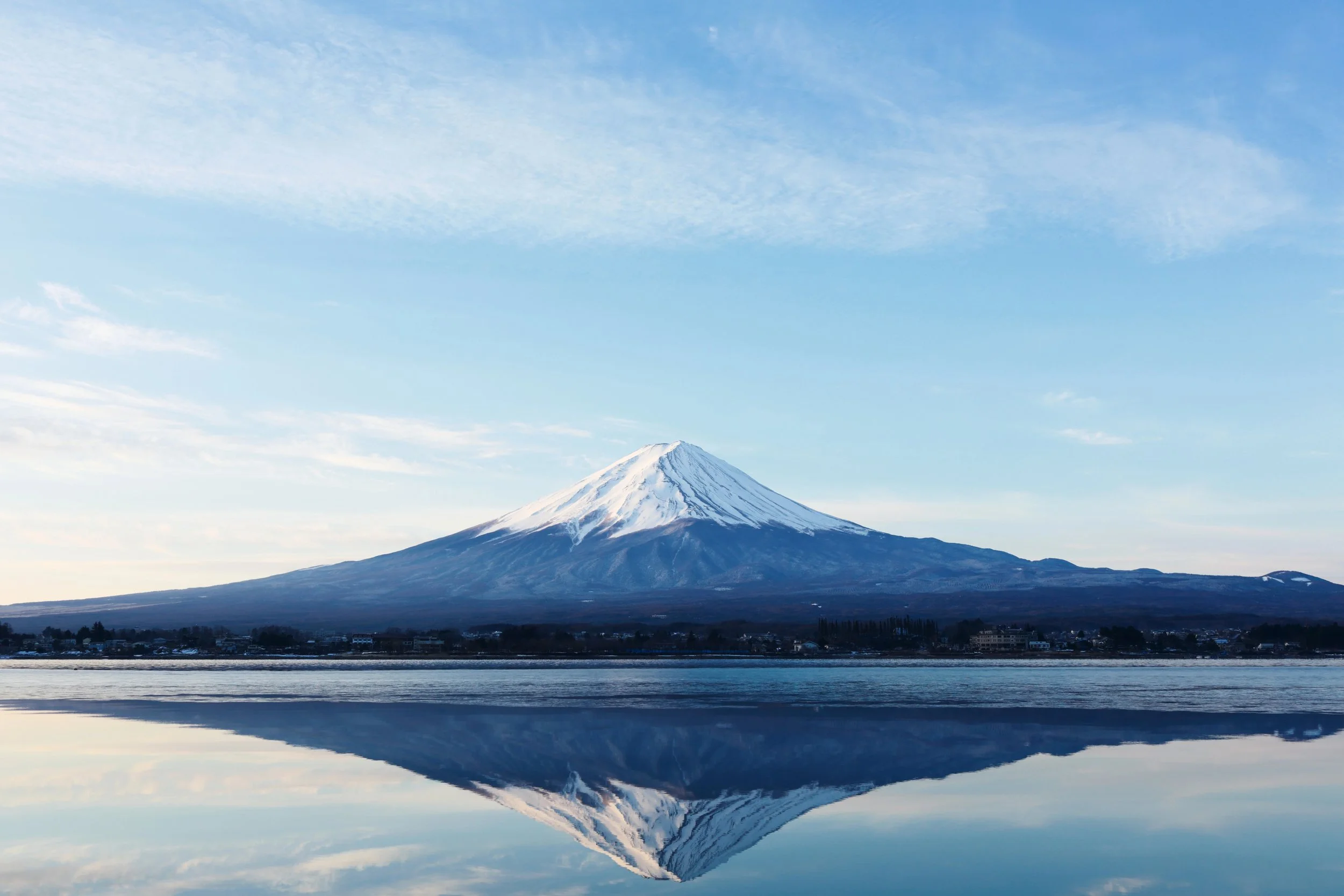
Want to ready your team for a challenge?
The start of any project can feel ambiguous and even a little daunting. We’re usually facing a big, messy problem. It can feel like we’re standing in a dense fog, unsure which direction to go.
Without clarity on the questions we're trying to answer, it's hard to know which actions make sense. Jumping straight into action often means we're also jumping in with assumptions, and that opens the door to a whole set of new problems.
In a team setting, the risks are even greater. People may head off in different directions. And even if everyone is doing great work, misalignment leads to wasted time, duplicated effort, and missed opportunities.
Contact me.
awelsh@impracta.com
(269) 277-7726